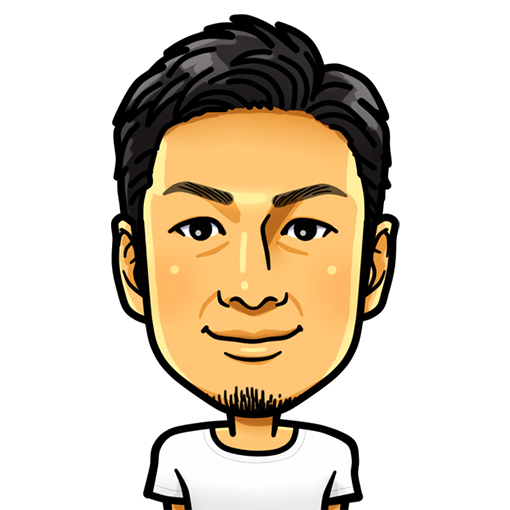
中規模、小規模工場がIoT導入に踏み切った理由と4つの事例
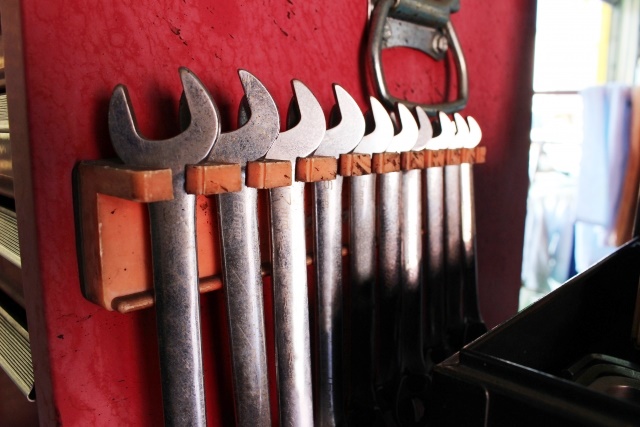
中規模、小規模工場でIoT導入をおこなうことになったきっかけは、次の様な経営課題にあります。
- 人手不足や従業員の負担を軽減したい
- 煩雑な事務作業をもっとシンプルにしたい
- 一部の従業員しかできない作業を他の従業員もできるようにして生産性を上げたい
- 製品の品質を上げたい
それぞれの工場によって抱える課題は様々ですが、「見えていない部分を見える化して、もっとシンプルに作業を進めていきたい」と考えた結果、IoTでの問題解決に踏み切った背景があります。
事例その1:作業者の動作をIoTで見える化し生産性アップ
岐阜県のとある硝子製造工場(従業員数80名ほど)では、作業者ひとりひとりにスマートウォッチを身に付けさせ、そこから発せられる信号データを自動収集しています。
信号データには作業工程ごとにかかった時間が記録されており、データが積み上がることで作業者ひとりひとりの得意とする工程、不得意とする工程が明らかになります。
また、その日の作業員全体のデータと硝子生産量のデータを突き合わせ日ごとに比較をしていくことで、生産性を上げるための人員配置の改善や、現場での作業者教育に役立てています。
IoT導入後の効果
- その日の製造計画に最適な人員と人数を配置できるようになり、製造コストが削減された
- 作業者ひとりひとりの能力が見える化され、得意な工程が多忙となった際に応援に入る体制が整った
- 作業者の仕事に対する意識改革が進み、自ら工夫したり改善の提案をしたりすることが増えた
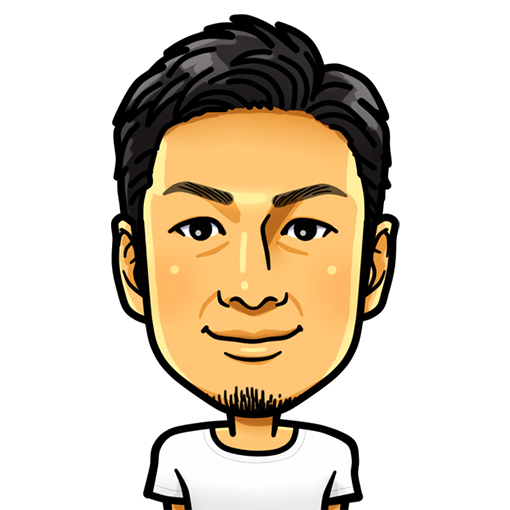
事例その2:データの一元化とクラウド利用で加工工程をどこからでも確認
東京都にある従業員数120名ほどの金属メッキ加工工場では、クラウドを利用した情報の一元管理で、少量生産・短納期の製品に対する作業を大幅に省力化しました。
具体的には、今まで別々に管理していた受注情報と生産管理情報を一括で管理できるシステムを導入し、どんな場所でも通信端末があれば情報が確認できる環境(クラウド)を整えています。
工場スタッフは作業状況をハンディ端末に入力し、無線でシステムに送信。
受注スタッフはお客様からの注文内容や納期などをパソコンからシステムに入力。
このように、生産状況と受注状況が1つのシステムで確認できることにより、事務所と工場間のやりとりが省力化。顧客への対応が大幅にスピードアップしています。
IoT導入後の効果
- 社内全員で1つのシステムを使うことにより、入力事務作業の重複がなくなり情報管理がスムーズに
- タブレット上から製作過程が確認できるようになり、営業社員の対応がスムーズに
- 情報を一元管理することで、納期遵守率や不良品対応など今後の経営課題となる情報が簡単に取り出せるようになった
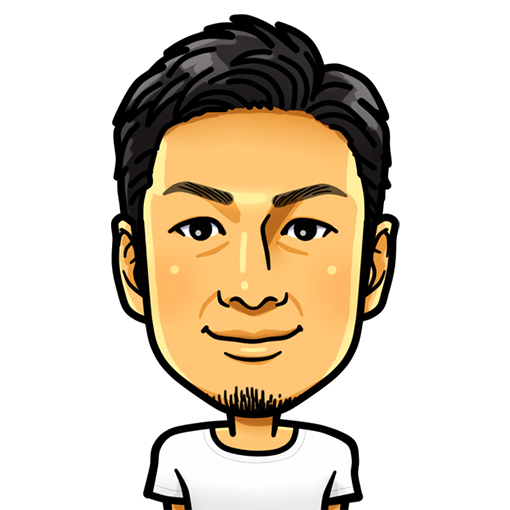
重要な情報がスタッフ全員で共有できていなかったり、紙のデータをエクセルに入力し直す二度手間が発生していたり、細かいところでロスが見受けられます。
受注側(事務所)と工場側でバラバラだった情報をIoTでひとまとめにすることにより、業務が円滑に進むようになった良い事例です。
事例その3:加工機の動きをIoTで見える化し稼働率20%アップ
茨城県にある精密機械加工工場(従業員数170名ほど)では、工場内の加工機それぞれに稼働状態が計測できる機器を取り付け、そこから収集したデータをネットワーク上で閲覧できるようにしています。
加工開始時間、加工終了時間、加工数、作業手順、進捗状況、エラー情報など、その日に動いていた加工機がどんな状態だったか?
このようなデータを積み重ねることで、無駄な作業をあぶり出して改善につなげることはもちろん、加工機械の状態をリアルタイムで把握し、トラブルに即対応することが可能となりました。
IoT導入後の効果
- 各加工機ごとの作業手順を見える化したことにより、担当者でなくとも投入部品の進度管理ができるようになった
- 工場と管理部門に大型モニターを取り付け、機器から送られてくる稼働状況をリアルタイムで従業員が確認することにより、意識向上につながった
- 作業指示待ちなどの無駄な時間がカットされ、設備稼働率が20%アップ
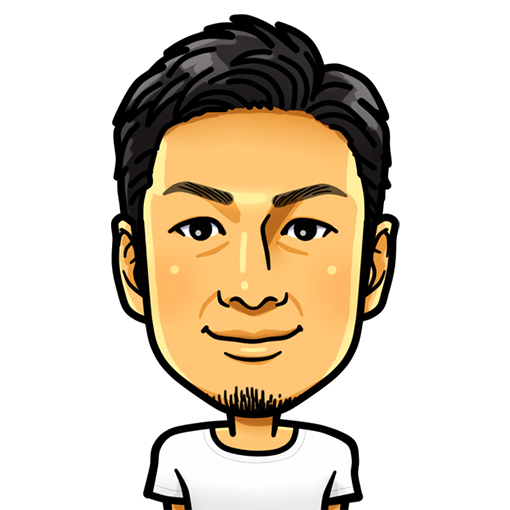
加工機械自体は従来のものをそのまま使い、それに対応する測定器とシステムを導入したことでIoT環境を整えています。
事例その4:作業マニュアル作成を紙からツールへ移行し省力化
東京都にある従業員数40名ほどのプラスチック、ゴム加工工場では、新人作業者に渡すマニュアルを紙からオンラインツールに変更しました。
従来のマニュアルは、紙に図を描いたりして作成していたため時間がかかり、さらに内容が更新される度に印刷や差し替えの手間がかかるなど非効率的でした。
それをオンライン上で作成できるツールに切り替え、実際の作業工程をスマホ等で撮った写真に説明文を付けてマニュアル化。
素早く簡単にマニュアル作成ができるようになり、引き継ぎ作業の省力化が実現しました。
IoT導入後の効果
- 紙のマニュアルに比べて情報検索が容易になり、作業者の作業効率が上がった
- オンラインマニュアルのため、最新の内容が常に作業者に行き渡るようになった
- 成功例、失敗例など様々な画像をマニュアルに載せておくことで、新人作業者の理解度が上がった
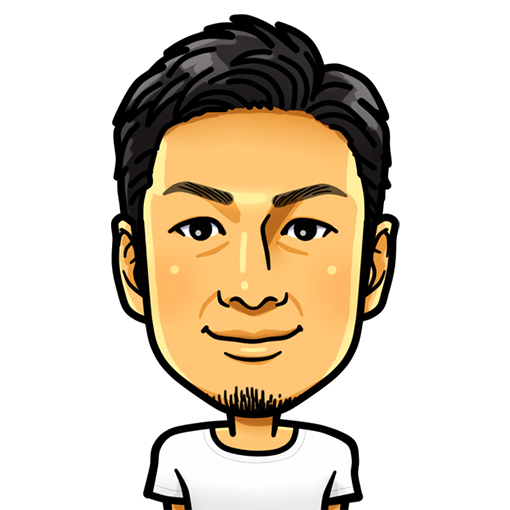
ですがその作成や配布に時間がかかってしまっては、肝心の製造の時間が削られてしまいます。
こういった「製造以外に発生する作業の省力化」に目を向けることで、小規模な工場でもIoT化による経営改善が可能になります。
※これまでの事例の参考「IoTユースケースマップ」より
中規模、小規模工場がこれからIoT化するために必要なこと
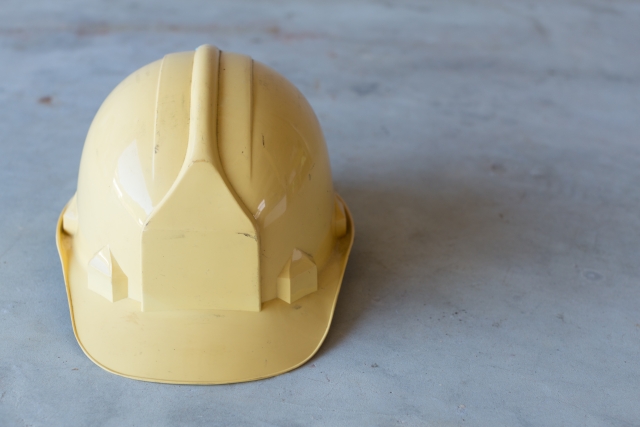
ここまでの4つの事例を見ていくと、工場の機械そのものを取り替えずともIoT化ができると感じたのではないでしょうか?
従来の機械でも取り付けられ作動するセンサ、インターネットにつながれば操作ができるシステムなど、中規模、小規模の工場が取り入れやすいIoT製品は日々登場しています。
それらの存在に気付くか?そして、自分事として捉えられるかどうか?工場経営者の手腕が試されるのがIoT活用です。
さらに言うならば、工場が抱える問題をIoTで解決しようと試みる前に「自社のネットワーク環境の全体像をきちんと理解すること」が大切です。
- 導入したいシステムは事務所のパソコンの性能で正常に動くのか?
- 何年も前に契約したインターネット回線だが、これからのIoT計画に適しているのか?
- 情報に対するセキュリティ対策は施されているのか?
このように、まずは工場内のネットワーク環境をきちんと経営者が把握し、適切に整えていくことで、IoT活用が不安なく進めていけます。
「機械の動きの見える化」「情報一元化システム」といったように、導入するアイテムが注目されがちなIoTですが、実はその土台を支えるのはネットワーク環境です。
1年以上ネットワーク通信費を見直していない、契約内容が分からない、何の通信サービスにいくら支払っているのか把握できていない。
もしも現在このような状態であるならば、まずはIoT導入の前に基本のネットワーク環境を見直すことをおすすめします。
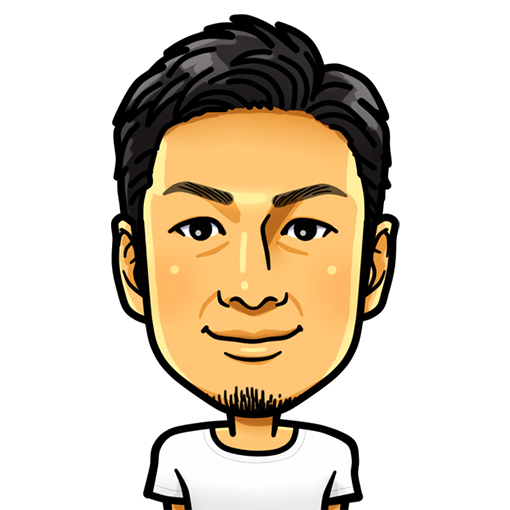
この3つの要素を揃えて、これからの時代にマッチしたスマートな工場を創り上げていきましょう。
ここ数年で国内の工場が次々と導入に踏み出しているIoTですが、具体的にどんな事例があるのか気になっている経営者の方も多いのではないでしょうか?
大規模な工場に限っての話で、小規模な工場には関係ない?
ITに強い従業員がいてこそ導入できるものではないのか?
そもそもIoTを導入すると、現場にどんなメリットがあるのか?
一筋縄では行かないイメージの強い工場のIoT化を、すでにおこなった所ではどのような結果が出ているのでしょう。
中規模、小規模でもIoT化した工場の事例を紹介しながら、ゼロからIoT化に取り組む場合に「まず始めるべきこと」についてもお伝えしていきます。